3D Printed Shoe
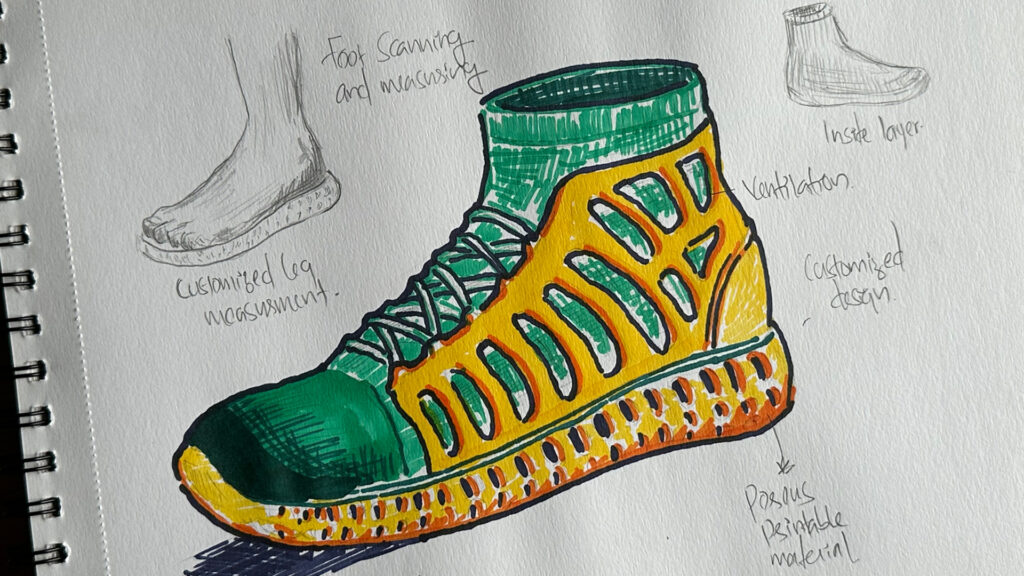
The manufacturing and technical details of 3D-Printed Custom Fit Footwear leverage the unique capabilities of 3D printing technology to provide personalized, high-performance shoes designed for each individual’s specific foot shape and gait. Here’s an overview of the process and the technology behind this innovative approach to footwear:
Manufacturing Process
1. Foot Scanning:
2. Biomechanical Analysis:
3. Design Customization:
4. 3D Printing:
The shoe components are 3D printed using advanced materials. The sole may be printed with a gradient of materials that vary in density, providing softer cushioning where needed and firmer support in other areas. The upper part can be printed from a flexible, breathable mesh that conforms to the foot.
5. Assembly:
Technical Specifications
1. Materials:
Sole: A combination of TPU (Thermoplastic Polyurethane) for flexibility and durability, and a graded rubber compound for traction.
Upper: A breathable, flexible mesh possibly incorporating recycled plastics or bio-based materials for sustainability
2. Printing Technology:
SLS (Selective Laser Sintering) or Multi Jet Fusion (MJF) for the sole, allowing for complex structures and material gradation.
FDM (Fused Deposition Modeling) or DLP (Digital Light Processing) for the upper, providing detailed textures and a snug fit.
3. Design Features:
Adaptive Cushioning: Customized zones of cushioning based on pressure point analysis.
Support Structures: Arch support and heel cup tailored to the wearer’s biomechanics.
Ventilation: Strategically placed ventilation zones in the upper for optimal breathability.
Interlocking Patterns: For the sole, enhancing flexibility and adaptability to various terrains.
Potential Challenges
• Material Longevity: Ensuring that the 3D printed materials withstand long-term wear and environmental conditions.
• Production Speed: Balancing the personalized manufacturing process with efficient production times.
• Cost: Managing costs to make the technology accessible while ensuring high quality and durability.
The concept of 3D-Printed Custom Fit Footwear represents a significant shift towards personalization in the footwear industry, offering unprecedented comfort and performance tailored to each individual’s needs. By overcoming the technical and manufacturing challenges, this approach has the potential to redefine how shoes are designed, manufactured, and sold.